control valves are pivotal in managing the flow and pressure within pipelines, ensuring that operations proceed smoothly and efficiently. However, just like any other piece of machinery, control valves can wear out, malfunction, or break down. When this happens, it’s crucial to address these issues promptly to minimize downtime and maintain productivity. In this blog, we’ll explore the significance of timely control valve system repair and how it can help keep your operations running at optimal levels.
Understanding Control Valve Systems
What Is a Control Valve System?
A control valve system consists of one or more valves used to control the flow rate, pressure, temperature, or level of a fluid in industrial processes. These systems are crucial for maintaining the desired conditions within a process, making them essential for product quality and operational safety.
Why Is Proper Maintenance Crucial?
Regular maintenance and timely repairs of control valve systems are essential because they:
- Ensure consistent product quality
- Prevent failures that can lead to production halts
- Reduce the risk of safety hazards in the workplace
The Impact of Control Valve System Failures
Production Delays and Downtime
When a control valve fails, it can cause immediate halts in production lines, leading to significant delays and potential losses in revenue. Downtime not only affects the bottom line but can also disrupt supply chains and damage customer relationships.
Safety Risks
Malfunctioning control valves can pose serious safety risks, especially in industries dealing with hazardous materials. Overpressure or uncontrolled flow can lead to accidents and environmental hazards.
Increased Operational Costs
Frequent breakdowns and emergency repairs can inflate maintenance costs. Moreover, inefficient control can lead to increased energy consumption and waste of materials.
How Timely Repairs Minimize Downtime
Quick Identification and Response
Implementing a routine inspection schedule helps in the early identification of potential issues before they lead to system failures. Recognizing signs such as leaks, unusual noises, or performance drops allows for prompt intervention.
Professional and Efficient Repairs
Working with skilled technicians who specialize in control valve systems can ensure repairs are done quickly and correctly. This minimizes the time your operations are disrupted and reduces the likelihood of recurring problems.
Preventive Maintenance
Regular maintenance not only fixes existing issues but can also prevent future ones. This proactive approach keeps systems running smoothly and extends the lifespan of your equipment.
Enhancing Productivity with Effective Control Valve Maintenance
Improved System Reliability
Regularly maintained and promptly repaired control valve systems are less likely to fail unexpectedly. This reliability ensures that processes run continuously without unscheduled interruptions, directly enhancing productivity.
Optimal Resource Utilization
Well-maintained control valves operate more efficiently. They ensure that resources, whether gas, water, or chemicals, are used optimally, reducing waste and operational costs.
Consistent Product Quality
Stable and controlled process conditions lead to uniform product quality. This consistency is crucial for maintaining customer satisfaction and brand reputation.
Best Practices for Control Valve System Maintenance
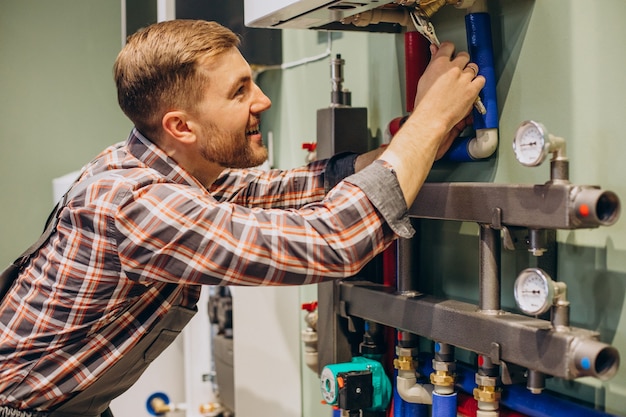
Routine Inspections
Regularly check control valve systems for signs of wear and tear. This includes looking for leaks, listening for strange sounds, or monitoring for performance issues.
Timely Repairs
Address identified issues immediately to prevent them from worsening. Delaying repairs can lead to more severe problems that are costlier and more time-consuming to fix.
Use of Quality Parts
During maintenance or repairs, use high-quality replacement parts that meet or exceed the original specifications. This ensures durability and performance, reducing the likelihood of future failures.
Training and Awareness
Train staff on the basics of control valve operation and maintenance. An informed team can better identify early signs of trouble and take appropriate action.
Leveraging Technology for Maintenance Management
Automation Tools
Use automation technology to monitor control valve conditions in real time. These tools can alert you to changes in performance that may indicate a need for maintenance or repair.
Data Analysis
Regularly analyze data collected from control systems to identify trends that may predict potential failures. Predictive maintenance can be scheduled at convenient times to avoid disrupting production.
Continuous Improvement
Use insights from maintenance records and performance data to continuously improve your control valve maintenance strategies. This ongoing refinement can lead to better overall system performance and reduced downtime.
Conclusion
Control valve systems are integral to maintaining the efficiency and safety of industrial processes. By recognizing the importance of timely repairs and regular maintenance, businesses can significantly reduce downtime and enhance productivity. Adopting best practices and leveraging modern technology for maintenance management can lead to more reliable operations, optimal resource utilization, and consistent product quality.
Investing in the health of your control valve systems is not just about fixing problems but about proactively creating a more efficient, safe, and productive operation. Keep your systems in top shape, and they will support your business goals for years to come.
Note:- To read more articles visit on kinkedpress.